What is a hazard?
A hazard, very simply put, is the potential for harm.
Pretty broad definition, huh? Well to put it into the perspective of an employee/employer, OSHA states it best, "a hazard often is associated with a condition or activity that, if left uncontrolled, can result in an injury or illness." Remember, identifying hazards (better yet, eliminating or controlling them) as early as possible can help prevent injuries or illnesses from happening.
One way this is done is through a 'Job Hazard Analysis' (JHA)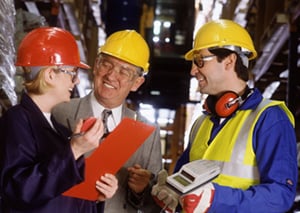
You may have heard the phrase job hazard analysis (or JHA), at your work before, or maybe you have seen/heard elsewhere. But some of you may be wondering what exactly a JHA is, what its used for, or who needs one? Well, we will discuss all of these topics but for now, lets take a moment and explain what exactly is a job hazard analysis.
A job hazard analysis is a procedure that identifies hazards before they occur. It aims to integrate preferred safety principles into the operation of the job or task. Basically, its a risk assessment that includes the safest way to do something. Once you have identified the hazards, the idea is to take steps to eliminate or reduce them to an acceptable risk level.
Why is it important?
Honestly, because conducting a JHA is one of the best ways to determine and establish proper work procedures. Many workers in the US are injured and even killed at work and proper safety measures and procedures help prevent workplace injuries and illnesses. Looking at your workplace operations, establishing proper job procedures, and ensuring that all empoyees are trained properly are ways to eliminate and prevent hazards in the workplace.
A job hazard analysis is likely to result in:
- Fewer worker injuries and illnesses,
- Safer, more effective work methods,
- Reduced workers' compensation costs,
- Increased worker productivity.
A JHA can also be a valuable tool for training new employees in the steps required to perform their jobs safely.
You may wonder who needs a JHA? Or who benefits from them? It could be argued, virtually any company could benefit from a JHA. It is designed to produce nothing but positive results, so virtually any company could implement one. But of course, there are companies that absolutely NEED a JHA (due to high hazards in the very nature of the work), and other specific industries that could implement one to make sure a safe environment stays that way. A job hazard analysis most benefits the following:
- Jobs with the highest injury or illness rates
- Jobs with the potential to cause severe or disabling injuries or illnesses, even if there is no history of previous accidents
- Jobs in which one simple human error could lead to a sever accident or injury
- Jobs that are new to your operation or have undergone changes in processes and procedures
- Jobs complex enough to require written instructions
Getting started
Where do you begin? It can seem like a daunting task before you, but luckily OSHA has helped lay out a 5 step outline for creating a JHA.
- Involve your employees
- This is very important. Employees have a unique understanding of the job, and this knowledge is invaluable for finding hazards. It will help minimize oversights, ensure a quality analysis, and increases "buy in" from employees because they share ownership in the safety and health program.
Review your accident history
- Your worksite's history of accidents and occupational illnesses
- Losses that required repair or replacement
- Any "near misses" - events in which an accident or loss did not occur, but could have
- These events are indicators that the existing hazard controls (if any) may not be adequate and deserve more scrutiny.
Conduct a preliminary job review
- Discuss with your employees the hazards they know exist in their current work and surroundings.
- Brainstorm with them for ideas to eliminate or control those hazards.
- If any hazards exist that pose an immediate danger to an employee's life or health, take immediate action to protect the worker.
- Any problems that can be corrected easily should be corrected as soon as possible. (Do not wait to complete your job hazard analysis)
List, rank, and set priorities for hazardous job
- List jobs with hazards that present unacceptable risks (those most likely to occur and with the most severe consequences). These should be your first priority for analysis.
Outline the steps or tasks
- Nearly every job can be broken down into job tasks or steps.
- When beginning a JHA, watch an employee perform the job and list each step as the worker takes it. (Sometimes it helps to record video of the job task for later reference)
- Don't get overly detailed; avoid breaking down the steps into so much detail that it becauses unecessarily long, or too broad to not include basic steps.
- Afterwards, review the job steps with the employee to make sure that you have not omitted something.
- Remember, you are evaluating the the job itself and not the employee's job performance.
How to identify hazards
Your main goals in an JHA are to discover the following:
- What can go wrong?
- What are the consequences?
- How could it arise?
- What are the other contributing factors?
- How likely is it that the hazard will occur?
OSHA has provided us with information on what "good hazard scenarios describe":
- Where it is happening (environment)
- Who or what it is happening to (exposure)
- What precipitates the hazard (trigger)
- The outcome that would occur should it happen (consequence)
- Any other contributing factors
Rarely is a hazard a simple case of one cause to one effect. More often, it consists of many factors lining up a certain way to create the hazard.
After you have reviewed your list of hazards, you must consider what methods will reduce (control) or eliminate them. Engineering controls that physically change a machine or work environment to prevent exposure to the hazard are the most effective. If this is not feasible, administrative controls (such as changing the way employees do their jobs) may be suitable.
Make sure to periodically review your JHA, to keep it current and help reduce accidents. In the event that a "close-call" or even an injury/incident occurs, be sure to review the JHA and discuss with your employees to ensure that all are aware of the methods, procedures, and protective measures.
Be sure to keep an eye for the next article, where we will discuss the second part of this topic and include detailed information on 'common hazards', 'hazard control measures', and a sample JHA!
In the meantime, remember if you have any JHA-related questions or are interested in more information on implementing a JHA for your company, contact STS's consulting professionals for assistance today!
Simply interested in safety training?
Click below for more information!