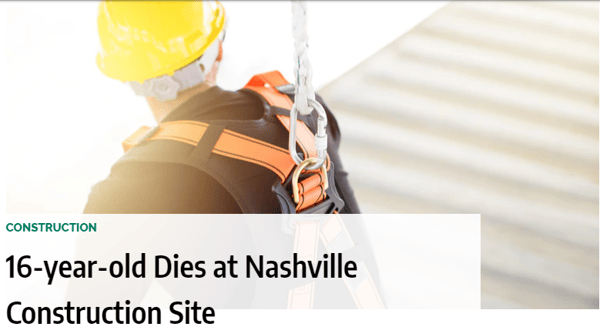

Tags: fall protection in construction, Fall protection training, OSHA fall protection
Today's blog article comes from Carmen Dexter at LawnStarter.com. They "bring you the best lawn services, all at the click of button." Whether you are a lawn care professional or simply looking to become more informed on common safety issues faced by those in lawn care services, please enjoy this article.
Thank you again LawnStarter for providing this information!
By Carmen Dexter
Landscaping is dirty work! It’s also dangerous. More than 6,000 people are injured while mowing their lawn each year, and a number of those accidents involve children. Many of those kids end up losing a limb or worse. That’s why so many homeowners hire a professional for lawn care. But even the seasoned landscaper isn’t immune from the hazards of the industry.
About 13,000 injury or illness cases in the landscaping industry are reported to the government each year. Some are preventable … if you know what to do to keep disaster at bay.
Landscaping is one of the country’s most dangerous jobs, according to the Bureau of Labor Statistics, and traffic is a major hazard. Accidents happen while transporting equipment to a job site or working near traffic. Lawn care workers have died after falling out of the back of the truck they were riding in. Equipment not properly secured in a vehicle has fallen on a crew member. A car struck a landscaper, and the driver said he didn’t see him.
Take steps to avoid these accidents:
● Never transport workers in a truck’s cargo area.
● Make sure equipment is secure before moving.
● Encourage all workers to practice safe driving.
● While working near the street, landscapers should wear bright clothing and safety vests.
● Know the address of your work site. If there’s an accident, emergency crews need to know where to go, as quickly as possible.
Contact with machinery or equipment is high on the list of accidents for lawn care workers. Operating mowers, trimmers, shredders, chippers, rotating blades, and chainsaws requires concentration. A few extra steps beforehand can help prevent injury. Dress in close-fitting clothing and leave the jewelry at home. Wear nothing that could get caught in the equipment. Keep clear of blades when working and maintain tools regularly to keep them in good working condition. Put on sturdy boots, gloves, safety goggles, and earplugs. Also, remove debris from the lawn before you start mowing. Pick up rocks, bottles, and anything that could get caught in the mower and thrown around.
The long hours landscapers spend in the sun can lead to heat stress or even skin cancer. Heat sickens thousands of outdoor workers each year by causing excessive sweating. That can bring about cramps, exhaustion, or heat stroke. Lawn care companies can help prevent these illnesses by providing plenty of fresh water for employees, allowing breaks as needed, and offering shade if possible. Workers can help themselves by frequently drinking small amounts of water and wearing a hat. It's also important to avoid caffeine and large amounts of sugar, as they can lead to dehydration.
One danger endemic to the landscaping industry is exposure to pesticides. These chemicals can enter the body by mouth, through the skin and eyes, or as vapors inhaled into the lungs.
Pesticides can cause a variety of health problems, depending on the person and the level of exposure.
Take these steps to protect yourself:
● Wear protective clothing.
● Don’t spray above your head, where the drops might fall back on you.
● Stay out of areas that have just been sprayed.
● Close container lids tightly.
● Use caution when handling pesticide containers.
● Bathe and put on clean clothes as soon as you get home.
These are some of the main safety issues facing lawn care companies and their employees. Accidents happen, and the best way for a company to avoid problems and reduce their severity is to train workers, provide a safety manual, and insure themselves so that everyone is covered.
The Hazardous Waste Operations and Emergency Response (HAZWOPER) standard requires employers to provide training to employees who provide emergency response services during releases of hazardous substances, 29 CFR 1910.120(q)(6). The level of training the employer must provide depends on the role the employee will perform in a response.
The difference between a hazmat responder and a hazmat technician
Employees must be trained to the first responder operations level if they will be part of the initial response for the purpose of protecting persons, property, or the environment from the effects of the hazardous substance release. Employees who respond for the purpose of actually stopping the release must be trained as hazardous materials technicians.
Responders at the operations level must receive at least eight hours of training or have sufficient experience to objectively demonstrate certain competencies listed in the HAZWOPER standard.
Hazardous materials technicians must receive at least 24 hours of training at the operations level and satisfy certain additional competencies listed in the standard. [See 29 CFR 1910.120(q)(6)(ii) and 1910.120(q)(6)(iii)]
In addition, the HAZWOPER standard requires that operations and technician level employees "receive annual refresher training of sufficient content and duration to maintain their competencies, or shall demonstrate competency in those areas at least yearly." 29 CFR 1910.120(q)(8).
It is important to note that training required under 1910.120(q) is dependent upon the anticipated duties and functions of the responder. Training and competencies must be consistent with each employee's anticipated role. For example, certain course topics could be suitable for operations level or hazmat technician refresher training, however they may not provide proper refresher training for personnel assigned as incident commanders (individuals who assume control of the incident scene).
Furthermore, an employee trained as a hazmat technician for responses to certain types of emergencies (e.g., agricultural emergencies) may not be adequately trained to respond to other types of emergencies (e.g., chemical releases or spills).
Using computer-based training as refresher training
Computer-based training may meet some refresher training requirements, provided that it covers topics relevant to workers' assigned duties. It must be supplemented by the opportunity to ask questions of a qualified trainer and by an assessment of hands-on performance of work tasks.
In OSHA's view, self paced, interactive computer-based training can serve as a valuable training tool in the context of an over-all HAZWOPER training program. However, use of computer-based training by itself would not be sufficient to meet the intent of the standard's various training requirements. Their position on this matter is essentially the same as their policy on the use of training videos, as the two approaches have similar shortcomings. OSHA urges employers to be wary of relaying solely on generic "packaged" training programs in meeting their training requirements. Training required under HAZWOPER includes site-specific elements and should also to some degree be tailored to workers' assigned duties.
In order for the training to be effective, trainees must have the opportunity to ask questions. This requirement could be met by providing a telephone hotline so that trainees will have direct access to a qualified trainer. The trainees' mastery of covered knowledge and skills must also be assessed. It is not clear whether "validation of course-work completion" as described in the advertisement you enclosed means that this particular computer-based training program actually assesses whether workers have mastered the covered material.
Hazardous waste operations can involve many complex and hazardous tasks. It is imperative that employees be able to perform such tasks safely. Thus, auditing of worker performance is required for all types of HAZWOPER training. In the case of refresher training, this requirement for auditing of worker performance could be addressed during periodic safety meetings.
Traditional, hands-on training is the preferred method. The purpose of hands-on training, for example in the donning and doffing of personal protective equipment, is two-fold: first, to ensure that workers have an opportunity to learn by experience, and second, to assess whether workers have mastered the necessary skills. The employer may determine that hands-on training is unnecessary for a given refresher course. However, if an employer elects not to use hands-on training in their refresher course, the employer must first assess the employees' skill level, and ensure that workers remain competent in their current and any newly assigned duties.
In conclusion, it is possible in some cases to use computer-based training in meeting the refresher training requirements of 29 CFR 1910.120(e)(8), provided that the computer-based training covers topics relevant to workers' assigned duties and is supplemented by the opportunity to ask questions of a qualified trainer, as well as an assessment of worker skill degradation through auditing of hands-on performance of work tasks.
Refresher training done over different dates/time
Refresher training may be given in segments so long as the required 8 hours have been completed by the employee's anniversary date.
We also point out that 8 hours is a minimum requirement; many employers will find it difficult to cover all topics listed in the training requirements in the minimum allowable time. The competencies to be covered during training sessions may demand more than 8 hours. When developing training, employers must structure their refresher training based on the employee's expected job duties.
Consequence of missing your annual refresher training date
If the date for refresher training has lapsed, the need to repeat initial training must be determined based on the employee's familiarity with safety and health procedures used on site. This means if you haven't kept up your skills, you may need to repeat a full hazmat training course. If a full course is deemed not necessary, the employee should take the next available refresher training course. And as OSHA states it, "There should be a record in the employee's file indicating why the training has been delayed and when the training will be completed."
--From osha.gov
Tags: hazmat training, hazmat refresher
The Occupational Safety and Health Administration (OSHA) offers Outreach Training for 4 industries: Construction, General Industry, Maritime, and Disaster Site Work. OSHA has done well over the years to expand the reach of their programs to help workers become more knowledgeable about workplace hazards and their rights. Specifically, OSHA's Outreach Training Program provides training on the recognition, avoidance, abatement, and prevention of these workplace hazards.
The construction industry deserves a little extra attention as it accounts for about 1 in 5 worker deaths. The Focus Four hazards (falls, struck by object, electrocution, and caught-in/between) are especially dangerous. In fact, according to OSHA, eliminating the Focus Four would save over 600 workers' lives in America each year.
Here are OSHA's top violations as they relate to the construction industry and how you can learn more about/avoid them.
Designed to protect employees on walking/working surfaces with an unprotected side or edge above 6 feet.
1926.501(b)(13) - Residential construction.
1926.501(b)(1) - Unprotected sides/edges.
1926.501(b)(10) - Roofing work on low-slope roofs.
1926.501(b)(11) - Steep roofs.
1926.501(b)(4)(i) - Holes and skylights.
Employers are bound to protect construction workers from falls and falling objects while working on or near scaffolding at heights of 10 feet or higher.
1926.451(g)(1) - Each employee on a scaffold more than 10 ft above a lower level shall be protected from falling to that lower level.
1926.451(e)(1) - When scaffold platforms are more than 2 ft above or below a point of access. Cross braces shall not be used as a means of access.
1926.451(b)(1) - Working levels of scaffolds shall be fully planked or decked.
1926.451(g)(1)(vii) - Personal fall arrest systems or guardrails systems.
1926.451(g)(4)(i) - Guardrail systems shall be installed along all open sides and ends of platforms.
Covers general requirements for all ladders.
1926.1053(b)(1) - Portable ladder access.
1926.1053(b)(4) - Shall be used only for the purpose for which they are designed.
1926.1053(b)(13) - The top or top step of a step ladder should not be used as a step.
1926.1053(b)(16) - With structural defects.
1926.1053(b)(22) - An employee shall not carry any object or load that could cause the employee to lose balance and fall.
Now that you are aware of these heavily cited topics related to the construction industry, you can take steps in avoiding them. Your first might be to attend, or send your employees to attend a 10-hour OSHA training for construction. In this training, one will learn more about OSHA (and why we have the standards we do), health hazards in construction, personal protective and life-saving equipment, the Focus Four hazards (huge topic in construction), as well as some other construction related topics. For more information, or to attend our next OSHA 10 hour training for construction, click the button below. If you are in need of any other OSHA related safety training, visit our Training Services page to see what else Safety Training Services can offer you & your company.
As we close out May and therefore Electrical Safety Month, I wanted to share a bit of information for those not familiar with the training requirements for avoiding electrical hazards. Even if you are familiar with the requirements, allow this to serve as a quick reminder to verify that you are in compliance with your relevant OSHA standard.
For many of those in industry who face the risk of injury from electrical shock or other electrical hazards, you must be trained so that you are knowledgeable of these hazards and how to avoid them. Some occupations have a higher risk due to the nature of their job. In fact, OSHA has detailed out the typical occupational categories of employees that face a higher than normal risk of electrical accident. This includes the following:
*Workers in these groups do not need to be trained if their work or the work of those they supervise does not bring them or the employees they supervise close enough to exposed parts of electric circuits operating at 50 volts or more to ground for a hazard to exist.
For those who are on this list, but do not follow the expection list just above, training may be a necessary need to assist these employees in avoiding electrical hazards and a knowledgeable understanding of the potential of this energy. As you may surmise, proper precautions must be taken to guard against these hazards. Too many employees, too often, are victims of injuries (or worse) because they fail to take these proper precautions to guard against such hazards. Failure to recognize the hazard of contact with energized electrical equipment can be a fatal mistake.
Necessary Training Requirements for Electrical Safety &
Avoiding the Risk of Electrical Shock:
29 CFR 1910.332
www.OSHA.gov
Qualified employees are those permitted to work on or near exposed energized parts. Those not not deemed qualified persons, but whom risk similar electrical hazards, shall also be trained in and familiar with any electrically related safety practices. The different training requirements for qualified and unqualified employees are outlined below for reference.
"Qualified" employees must (at a minimum) be able to:
Training for "Unqualified" employees should cover (at a minimum):
Once again, as Electrical Safety Month comes and goes with the month of May, there is no better time to access your electrical safety needs. If you are in need of either electrical safety training or arc flash training, or simply have a question regarding these topics, contact Safety Training Services today. We look forward to assisting you with your electrical safety & training needs!
According to the United States Department of Labor’s Occupational Safety and Health Administration (OSHA), employees need to have protective footwear when working in places where they are exposed to the risk of foot injury. This may be due to falling, rolling or piercing objects and/or electric shock. There are many set standards that must be met for a pair of work boots to be considered safe.
Are you looking for a pair of safety boots? Do you know the qualities that these boots must possess? Here we will explain to you what these work boots safety standards are. It is very important that the boot you buy has the right qualities. This way it will serve you for a long time and keep you safe always.
The safety standards that the boot must meet will depend on the kind of job it is that you do. The industry safety requirements differ from one industry to the other and you need to be aware of what applies to you. You can learn about this in the infographic you will find here. When you spot a boot that you like, be sure to look at the specifications indicated under the sole, inside the shoe and in the ASTM labels. It is this information that will tell whether the boot is safe for use or not. With that said, here is what people in different occupations should look for in boots.
Look for boots that have a green triangle symbol. This symbol means that the boot has grade 1 sole and class 1 toe cap. These are resistant to punctures and will stand the prolonged exposure there is in these industries. The sole can walk well in rough places as well as protect you from pierce injuries whereas the shoe cap is capable of protecting the toes in case something heavy falls on the foot.
These are the areas where the boots will not be exposed to too much impact. For these, look for a yellow triangle which indicates that the shoe has grade 2 puncture resistant sole and class 2 toe cap. These are weaker compared to boots with green triangle but if you work in an industry that is not heavy duty they will help you.
If you handle electricity on a day to day basis and risk an electric shock, you need to get boots that have a white square with an omega (orange) symbol. This shows that they are insulated and will protect you from electrocution.
If you are one of these you should buy boots that have a yellow square with the letters SD written in green. These shoes will protect you from static charges.
Look for a sign that looks like a fir tree on a white background. This boot can protect from sharp objects that can cut like chainsaws.
By referencing the infographic below, you can see what these symbols look like and mean. For a wealth of more information about work boots & their safety standards, take a look at the aboutboot website: http://www.aboutboot.com/work-boot-safety-standards/. Be sure to check the boot you buy next before taking it home.
Tags: work boot, safety boot
OSHA recently announced this fiscal year's preliminary list of their "Top 10" most frequently cited workplace safety violations. Below, you will find the list as well some insight on OSHA's new approach to inspections and trends for 2016. In the coming weeks, we will be releasing blog articles written with the intent of showcasing these top violations, and how to avoid them.
Also, OSHA had announced that it will change the way it approaches inspections. The plan was to (starting this month, October 2015) emphasize quality over quantity. The idea was that OSHA would then be able to tackle more complicated, time-consuming inspections and therefore more impactful inspections. There is a bit of pressure under the current system to make the numbers, and hopefully with a new system, more meaningful and effective inspections can occur and lead to improved worker safety.
The last piece to note is about enforcement trends. As the number of inspections may change going into 2016 due to the changes in their approach to inspections, the trend of paying higher fines per citation has been continued into 2015 and may very well continue into 2016 seeing as the new system of inspections will focus on these more impactful inspections. Also to note on that subject is OSHA's Severe Violator Enforcement Program (SVEP) which saw an almost 25% increase from 2014 to 2015, and continues onwards to today. Lastly, many more OSHA inspections are brought about by employee complaints, as OSHA has reached out to employees directly and allows easier access for them to go online and reach out to OSHA. Unjustifed complaints come in, due to disgrunted employees or whatnot, but this can be reduced by creating good safety culture within their workplace. Expect this trend of more concerned employees reaching out to continue.
Tags: osha training, osha most cited, OSHA, osha compliance, osha top violations, osha safety, osha general industry training, osha safety topics, osha violations, osha safety training, osha violations 2015
Safety training is an important part of any business. Not just for those going into confined spaces or other hazardous atmospheres, but for those going into a formal office, a hospital, or anything in between. Safety training is a phrase often used to describe the training materials designed to teach occupational safety and health standards developed by various safety governing entities such as OSHA (Occupational Safety and Health Administration), ANSI (American National Standards Institute), EPA (Environmental Protection Agency), or DOL (Department of Labor). Employers in the United States have a legal responsibility to educate employees on all workplace safety standards and the hazards their employees may face while working on the job. Proper safety training, whether through the employer or a third-party contractor, meets this requirement.
For safety training to be successful, participants must be able to demonstrate knowledge of the standard and how it applies to their specific job. If presented correctly by a qualified trainer, it can promote a strong culture of safety in the workplace, one where veteran employees follow proper safety rules & guidelines and assist in promoting the same for new hires. This is achieved by both good, safety-conscious employees and solid trainers who keep employees engaged and keep their training program relevant and not too generalized.
But what happens when you neglect safety training at your workplace? In addition to a potential increase of the things listed above, here are a few times employers have felt the sting in their financial bottom line as well. Below, I have itemized OSHA citations reported in Jun-Aug 2015 for infractions of neglecting safety training for their employees. It's much cheaper to hire someone to do your training if you are unable to handle it yourself than to wait until OSHA hits you with related fines.
Company: Bigston Corporation
Inspection Site: Elk Grove Village, IL
Date of Findings: March 5, 2015
Type of Violation: Serious
29 CFR 1910. 134(k)(1): The employer did not provide respirator training that would ensure each employee could demonstrate knowledge of items in section (i)-(vii).
Penalty: $4,200.00
Company: Grimco Inc.
Inspection Site: Akron, OH
Date of Findings: June 3, 2015
Type of Violation: Serious
29 CFR 1910.147(c)(7)(i): The employer did not provide training to ensure that the purpose and function of the energy control program are understood by employees and that the knowledge and skills required for the safe application, usage, and removal of the energy controls are acquired by employees.
Penalty: $7,000.00
Company: Wilbert, Inc.
Inspection Site: Bellevue, OH
Date of Findings: February 2, 2015
Type of Violation: Serious
29 CFR 1910.174(c)(7)(i): The employer did not provide adequate training to ensure that the purpose and function of the energy control program was understood by employees.
Penalty: $7,000.00
Company: D.R. Diedrich & Co.
Inspection Site: Milwaukee, WI
Date of Findings: February 2015
Type of Violation: Serious
29 CFR 1910.174(c)(7)(i)(A): Authorized employee(s) did not receive training in the recognition of applicable hazardous energy sources, the type and magnitude of the energy available in the workplace, and the methods and means necessary for energy isolation.
Penalty: $6,300.00
Company: Ansley Metal Fabrication and Repair
Inspection Site: Donalsonville, GA
Date of Findings: March 26, 2015
Type of Violation: Serious
29 CFR 1926.761(b): The employer did not train each employee exposed to a fall hazard in accordance with the requirements of 29 CFR 1926.761.
Penalty: $4,900.00
Company: New Homes Construction, Inc.
Inspection Site: Medford, NJ
Date of Findings: February 12, 2015
Type of Violation: Serious
29 CFR 1926.503(a)(2): The employer did not assure that each employee exposed to fall hazards was trained by a competent person qualified in the areas specified in 29 CFR 1926.503(a)(2)(i) through (viii).
Penalty: $3,080.00
Type of Violation: Serious
29 CFR 1926.1060(a): The employer did not provide a training program for each employee using ladders and stairways, as necessary, which would train each employee in the procedures to be followed to minimize hazards related to ladders and stairways.
Penalty: $3,080.00
Company: Elite Storage Solutions, LLC
Inspection Site: Monroe, GA
Date of Findings: January 28, 2015
Type of Violation: Serious
29 CFR 1910.147(c)(7)(i): The employer did not provide training to ensure that the purpose and function of the energy control program are understood by employees and that the knowledge and skills required for the safe application, usage, and removal of the energy controls are acquired by employees.
Penalty: $7,000.00
Type of Violation: Serious
29 CFR 1910.157(g)(l): An educational program was not provided for all employees to familiarize them with the general principles of fire extinguisher use and the hazards involved with incipient stage fire fighting. The employer expected employees to use extinguishers to use extinguishers to fight incipient level fires, but did not implement a training program for the use of fire extinguishers.
Penalty: $5,500.00
As you can see, the above fine amounts aren't generally high enough amounts to warrant closing up your company's doors, but they will certainly impact your profitability. Even more important is the realization that after paying the fine, you still have to pay for the training as well. Which can effectively double the initial cost if you were to train your employees in the first place. That number wouldn't even have taken into consideration the potential increase of compensation claims, property damage, missed work, injuries, legal liabilities and everything else discussed earlier. Keep in mind too that OSHA has made it easy to anonymously tip them off to an unsafe workplace. One phone call or email can now much more easily give an inspector a reason to visit. You must always take employee complaints seriously. In the case of the last two sources, you can see that having two fines for training can add up. If you expect your employees to use the provided fire extinguishers, you must train them in proper usage and be sure to have someone designated to check them monthly. Last of note is the company that did not have a qualified person train their employees; be sure if you are training your employees yourself, or in-house, that you (or whomever is doing the safety training) is qualified to do so. You may decide it be best to hire an outside person or company to do your safety training, but again, be sure they are at a qualified level to conduct the training. If you have any questions about this subject, feel free to contact us here at Safety Training Services by clicking below!
Tags: osha training, safety, safety training, training, osha safety training, osha violations 2015
Tags: OSHA, awp training, forklift safety, aerial lift operator training, scissor lift safety, boom lift training, osha safety topics, osha violations
With the knowledge of where they came from out of the way, in no particular order, let's look at these 6 times a hard hat saved someone's life.
A 24-year-old man of Miami was working at a construction site, helping move a large sewer pipe via a huge pulley. The cable holding it up broke, and that huge pulley weighing several hundred pounds fell onto the worker's head. He suffered a large cut on his forehead and experienced back, leg, and head pain, but his hard hat prevented him from being severely injured or worse, death. (Source)
A salesman, alone and cutting down trees for firewood, was admittedly never a "hard hat guy." But his wife bought him a hard hat the year prior and insisted that he start wearing it. He was wearing it this day and I am sure he is glad he was, as a several hundred pound, 15 foot maple tree fell right onto his head after using the chainsaw to cut it down. He is certain that without that hard hat that day, he would not be around to tell the story. In fact, he is an advocate for all required PPE (personal protective equipment) necessary for the job. In his instance, gloves, chaps, and a hard hat are all part of what could save your life in a similar scenario! After a trip to the hospital for some stitches to address the small, but deep cut on his forehead, he was able to come out of the incident with but a simple battle scar.
A long distance runner from Oklahoma was on a disaster recovery trip in Texas helping with a church group who was there after a hurricane struck. This man was wearing a ball cap all week, cutting down trees with a chainsaw, when someone asked him to put on a hard hat. Again, all week he was in simply a ball cap, but this was the last day (probably one of the last trees, no less) when he decided he would put it on. The tree he was to cut (after putting on his hard hat) was in a seemingly perilous, or otherwise unsafe position and he made note of it. Put still, the tree had to come down and so he went to work on cutting his 'V' into the tree. As he started on the other side, the tree came tumbling straight down onto his head, and broke his pelvis, neck, and ribs. He had internal bleeding and a punctured lung. After fighting for his life for hours, and several operations within a week, he was unsure if he would ever be able to walk again. But after an emotional 13 weeks, he began to walk. Almost 10 years later, he just walked his daughter down the aisle. Today, he looks at the cracked hard hat that he was wearing that infamous day and remembers how it literally saved his life. (Source)
A power plant mechanic was tasked one day with working with a team to find a leaky pipe in a turbine pit. He, along with the other two in his team, had examined the pit from the outside only to find zero problems. This mechanic had volunteered to go into the turbine pit area and look at the other end for the leak. The way to get in, however, required some balance and stability. The mechanic was 6 feet tall and the narrow 4 foot ledge with only 4.5 feet of headroom had this guy ducking & bending to walk along the ledge. The short story of what happen next is that he bumped his head on a horizontal reinforcement piece on the ceiling of the generator apron he was walking on. The blow disoriented him enough to readjust the hard hat over his eyes and he fell 20 feet. In the process of the fall, he was bumped around and even lost his hard hat, but it stayed on him long enough to prevent serious injury or worse. A few gashes, bruises, and cuts appeared and his hard hat was shattered (both in front and back), but he was alive. After quick medical assistance, some rest at home, and a little physical therapy, he was able to retuen to work. The reason this particular accident is special is because the hard hat that fell off during this fall was held on momentarily by earmuffs during the blow which forced the hard hat to shatter. Regardless of the condition of the hard hat after the fact, the most important piece of information is that he was wearing it in the first place! (Source)
A 24 year old electrical contractor in Portland was working on a wind tower about 164 feet up when a 7 pound piece of plastic tubing fell from 65 foot above him and hit him on the head and shoulder. The man briefly lost consciousness and suffered spinal injuries while he was stretchered down a ladder and flown (in stable condition) to a hospital for medical care. This was another case where a person's hard hat probably prevented a fatality. (Source)
A demolition contractor was moving roofing materials from a platform onto the ground during the demolition of some old offices and warehousing. At roof height near him was a substantial piece of cast iron guttering which had been left unsupported for two days during the demolition. The guttering gave way and hit him and he broke his right arm, 7 ribs, and a vertebrae in his spinal column. He also received a cut to his head and punctured a lung. But again, for the sixth story on the subject, he survived due to the head protection he was wearing. (Source)
_______________
If you have a need for hard hats, or any other safety-related equipment, STS is ready to assist you in choosing the right equipment for your situation. Whether its PPE, air monitoring equipment, fall protection, first aid kits, AEDs, or anything in between, we are available to your company. We also offer OSHA related safety training, consulting work, and even are available to assist you with any rescue team needs as well as supplied air trailers available for rent! Contact us below to find out how our blended safety services can assist your company with any safety or OSHA related need.
Tags: hard hat
© 2025. Safety Training Services. All Rights Reserved.
8516 Henry Street, Highland, IN 46322 | (877) 724-2744