OSHA recently announced this fiscal year's preliminary list of their "Top 10" most frequently cited workplace safety violations. Below, you will find the list as well some insight on OSHA's new approach to inspections and trends for 2016. In the coming weeks, we will be releasing blog articles written with the intent of showcasing these top violations, and how to avoid them.
The "Top 10" for FY 2015 are: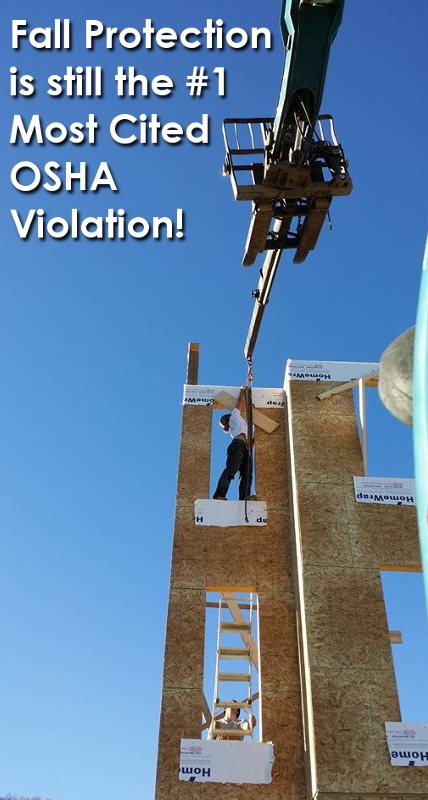
- Fall Protection (Construction)
- Standard Cited: 1926.501 - 6,721 violations
- Violations up (6,143 in FY 2014)
- Hazard Communication
- Standard Cited: 1910.1200 - 5,192 violations
- Violations up (5,161 in FY 2014)
- Scaffolding (Construction)
- Standard Cited: 1926.451 - 4,295 violations
- Violations up (4,029 in FY 2014)
- Respiratory Protection
- Standard Cited: 1910.134 - 3,305 violations
- Violations down (3,223 in FY 2014)
- Lockout/Tagout
- Standard Cited: 1910.147 - 3,002 violations
- Violations up (2,704 in FY 2014)
- Powered Industrial Trucks
- Standard Cited: 1910.178 - 2,760 violations
- Violations up (2,662 in FY 2014)
- Ladders (Construction)
- Standard Cited: 1926.1053 - 2,489 violations
- Violations up (2,448 in FY 2014)
- Electrical-Wiring Methods
- Standard Cited: 1910.305 - 2,404 violations
- Violations down (2,490 in FY 2014)
- Machine Guarding
- Standard Cited: 1910.212 - 2,295 violations
- Violations up (2,200 in FY 2014)
- Electrical-General Requirements
- Standard Cited: 1910.303 - 1,973 violations
- Violations down (2,056 in FY 2014)
Remember, these are what causes the majority of injuries and deaths as well as what a compliance officer would look for most often during inspections.
Also, OSHA had announced that it will change the way it approaches inspections. The plan was to (starting this month, October 2015) emphasize quality over quantity. The idea was that OSHA would then be able to tackle more complicated, time-consuming inspections and therefore more impactful inspections. There is a bit of pressure under the current system to make the numbers, and hopefully with a new system, more meaningful and effective inspections can occur and lead to improved worker safety.
The last piece to note is about enforcement trends. As the number of inspections may change going into 2016 due to the changes in their approach to inspections, the trend of paying higher fines per citation has been continued into 2015 and may very well continue into 2016 seeing as the new system of inspections will focus on these more impactful inspections. Also to note on that subject is OSHA's Severe Violator Enforcement Program (SVEP) which saw an almost 25% increase from 2014 to 2015, and continues onwards to today. Lastly, many more OSHA inspections are brought about by employee complaints, as OSHA has reached out to employees directly and allows easier access for them to go online and reach out to OSHA. Unjustifed complaints come in, due to disgrunted employees or whatnot, but this can be reduced by creating good safety culture within their workplace. Expect this trend of more concerned employees reaching out to continue.